Uniqa
Private Label
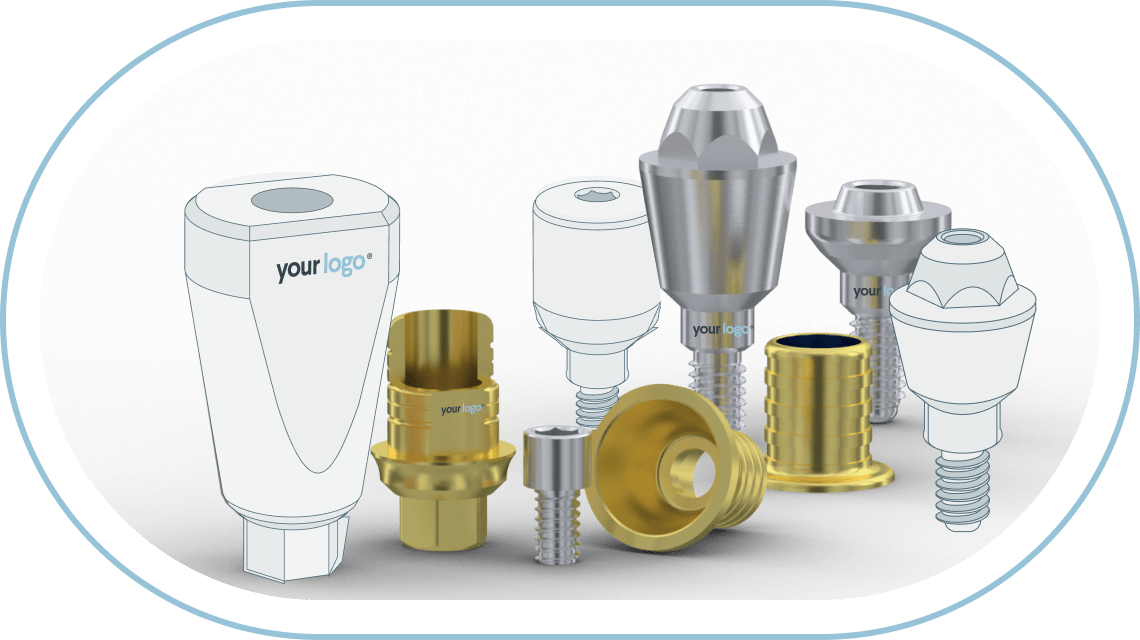
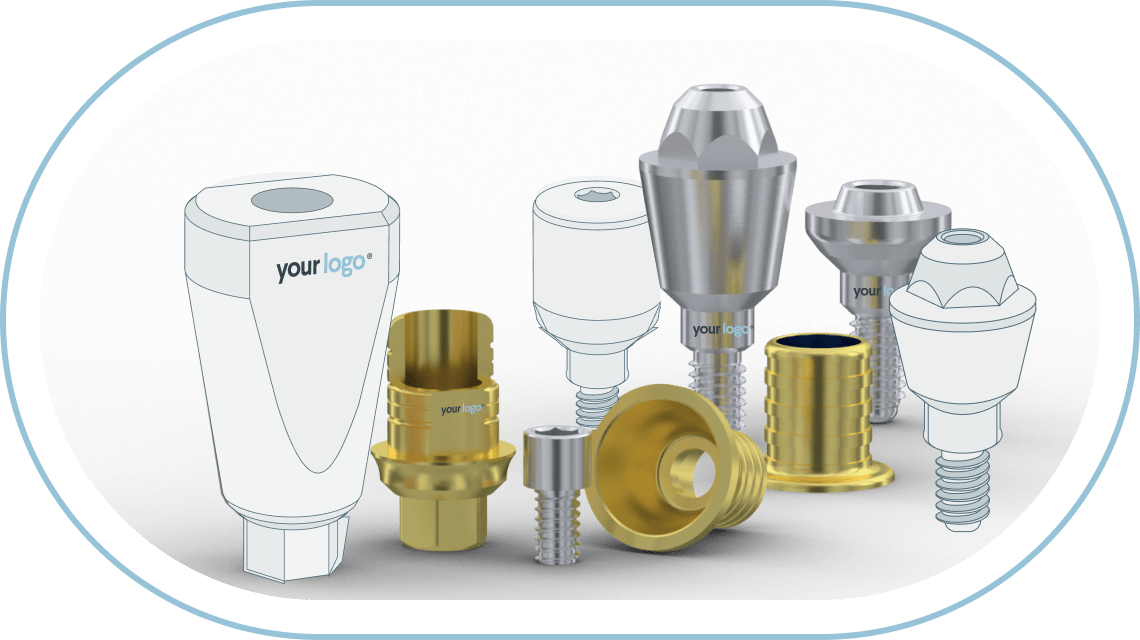
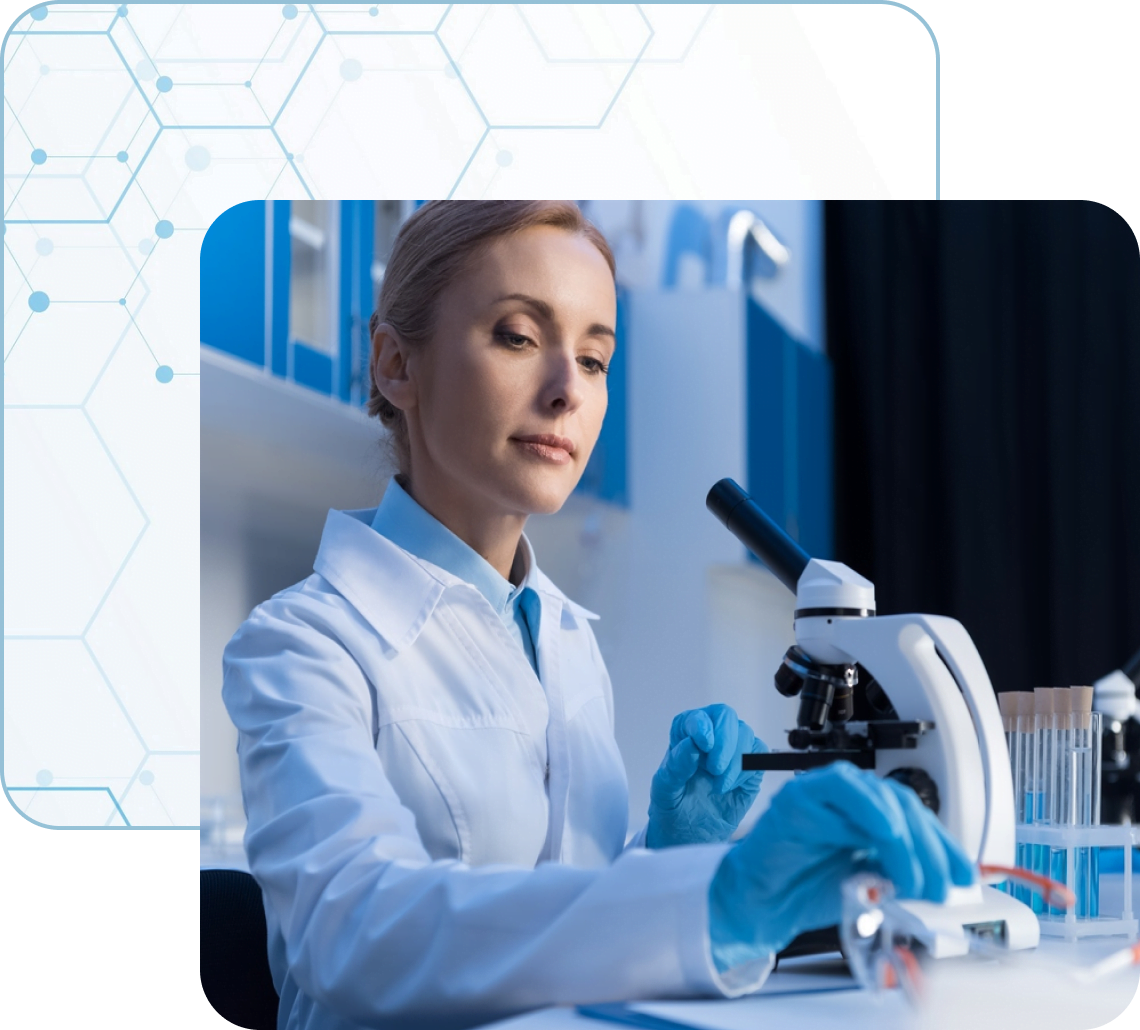
R&D is the first step to do product creation. Uniqa Dental’s research and development team consists of several generations of experienced dentists with deep knowledge and broad understanding of implantology and restoration processes. It’s not an exaggeration to say that they live and breathe everything related to dental practices. Moreover, having worked in the Israeli hi-tech industry for many years, they’ve accumulated vast experience in the chemistry, engineering, and electronic fields. This combination of excelling dental and technological experience provides high-end benefits to dentists who use Uniqa Dental products.
The timeline — from idea to implementation — is much shorter when innovation and creativity are enforced and supported by manufacturing capabilities.
After the development and manufacturing of a new product, it is extensively tested and corrected by Uniqa’s specialists to provide an improved version for the market.
Uniqa’s products are now offered by different implant companies.
You can look at our patents, and we can develop and test products for your company (per our R&D terms and conditions)
Today, Uniqa Dental is manufacturing implants and prosthetic parts for other implant companies who in turn, offer these products around the world. Uniqa Dental manages several manufacturing departments:
Uniqa Dental’s Pure&Porous™ process for surface (read more) formation of dental implants combines the advantages of two of the most usable surface treatment processes in dental practice:
- The highly developed surface porosity of the Alumina (or Sand) blasted, Large-grit, Acid-etched (SLA) Process
- The high cleanness of the Resorbable Blasted Media (RBM) process
The dental implants’ surface, after the Pure&Porous™ treatment, is as well structured as after the SLA process and as clean as after the RBM process.
At the same time, the Pure&Porous™ process is free from their drawbacks
- During the SLA process, residual particles remain on the surface as a result of sandblasting and the chemical solution used during surface treatment
- RMB results in weakly structured surface topography.
Uniqa Dental realizes the Pure&Porous™ process using its CSTTM approach to dental implants’ surface formation. The process consists of two main stages:
- To avoid surface contamination during blasting, we use biocompatible hydroxyapatite as the main component along with other calcium phosphates.
- We use gentle etching to remove blast residues and to create an optimal surface microstructure.
The Pure&Porous™ process has been running since 2012 and has been approved through tens of thousands of successful medical cases.
The Pure&Porous™ implants surface quality, as evaluated by Scanning Electron Microscope (SEM), Energy Distribution Spectrum (EDS), X-ray Photoelectron Spectroscopy (XPS), and optical profile measuring instruments, reveals highly developed surface porosity, and extreme cleanness of the surface.
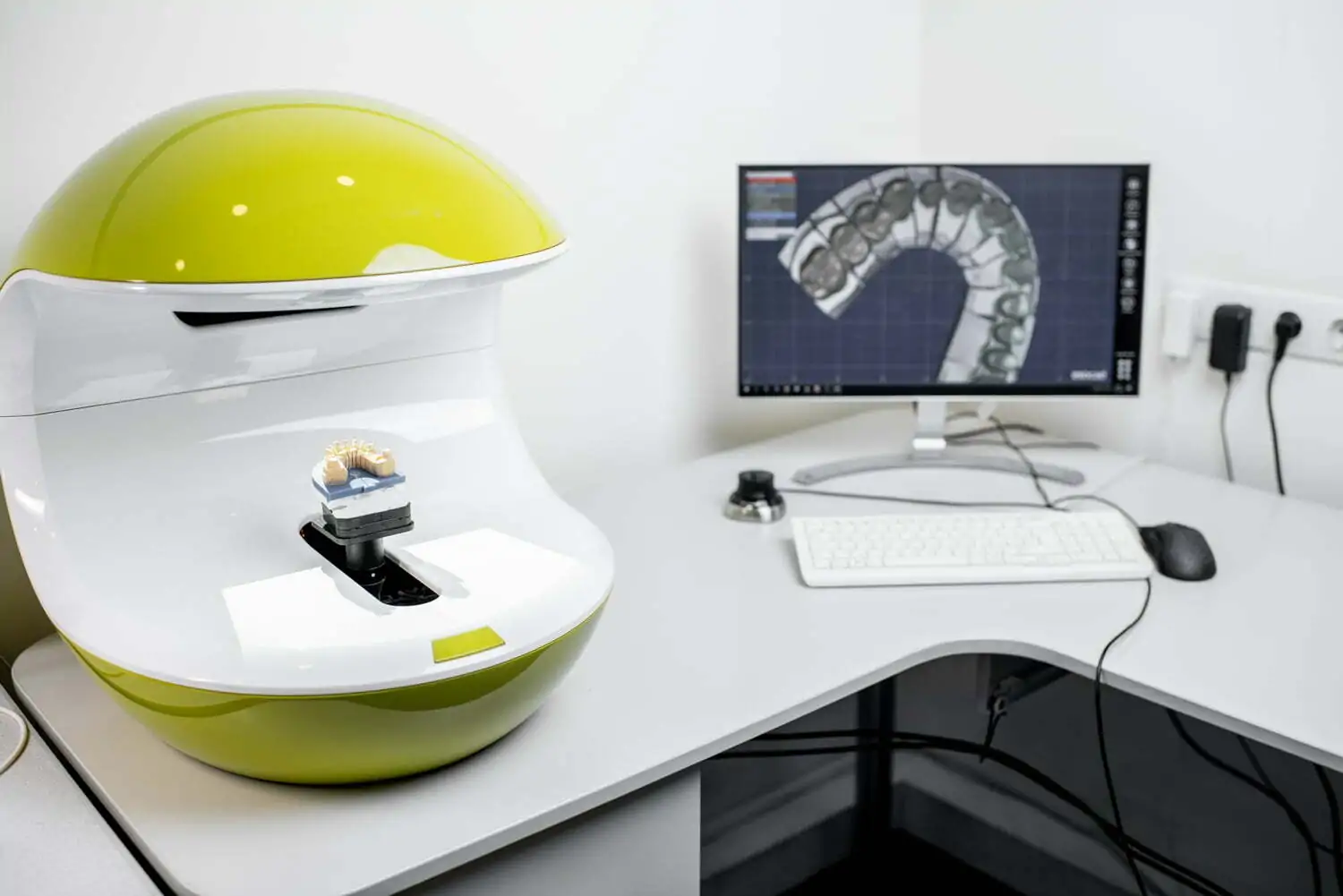
Uniqa Dental can lead you confidently into the exciting world of CAD/CAM implantology, with the most advanced screw-retained systems.
Designed by dentists for dentists, Uniqa Dental’s Restoration System is an advanced multi-unit system that provides clinicians with a comprehensive restorative solution, perfect for every case, that saves time, effort and ensures more satisfied patients.
Our innovative system features two lines of multi-unit abutments, advanced libraries for digitally scanning abutments with greater accuracy, and a variety of sleeves that enable dentists to perform successful and aesthetic restoration procedures on screw-retained systems. Because, when it comes to your patients, one appointment is always better than many!
At Uniqa Dental you will find multi-units, abutments, and other prosthetics parts for almost all popular implant connections
Here, we use the high-tech CNC SWISS Type equipment which allows high-quality products and large production volumes. High quality is assured through:
These three factors provide a high level of confidence to implant companies that do their manufacturing in Uniqa Dental facilities. As a result, end customers enjoy premium quality products based on well-established development.
There are implant companies that manufacture abutments and implant parts at different vendor facilities. The main issue with this method is that after several years, there is micro-movement in the patient’s mouth between the implant and the abutment connection. Let’s consider the following example:
Vendor A is manufacturing the following implant:
Implant connection is Internal Hexagonal 2.42mm were done with −+0.05mm, in this case, every implant from 2.37mm to 2.47mm will pass quality control.Vendor B is manufacturing the following abutment:
Abutment hexagonal connection with the same size 2.42mm with −+0.05mm tolerances, in this case, every abutment from 2.37mm to 2.47mm will pass quality control.
The fact is, this implant company will have created a gap of 0.1mm between the implant (2.47mm) and the abutment (2.37mm), which can lead to micro-movements in the future.
At Uniqa Dental we avoid this situation by manufacturing both parts at the same facilities and by testing them during production.
Based on an understanding of the possibilities and limitations of milling machines, we manufacture our screw restoration systems as titanium bases and multi-unit systems that, in combination with CAD/CAM technologies, provide simple and technological solutions for the laboratory and the dentist.
This is done so that the laboratory can use a high-precision abutment that was produced at the factory and which fully corresponds to its virtual version — the library/gallery. Otherwise, its manual modification can introduce severe errors in the final work.
We promote quality control for every product that we create and in every step of the process — from setup on the CNC machine to frequent tests during the manufacturing process and final tests post-manufacturing.
In addition, after initial tests are completed, the products go through another, independent team that conducts very strict quality tests, and should any issues arise, these products are sent back to production for improvement, or otherwise, rejected altogether.
Uniqa Dental uses highly accurate measurement equipment that guarantees true results. This equipment undergoes periodic calibration tests to assure the integrity of the results.
Implant surfaces are inspected at every step of production.
Tests like spectrum analysis, SEM, fatigue, sterilization, biocompatibility, and others are conducted in the most advanced laboratories in the world including NAMSA USA, The Ben Gurion Beer Sheva University, and The Technion in Haifa.
Uniqa DENTAL holds CE certificate, FDA510K, ISO 13485, ISO9001.
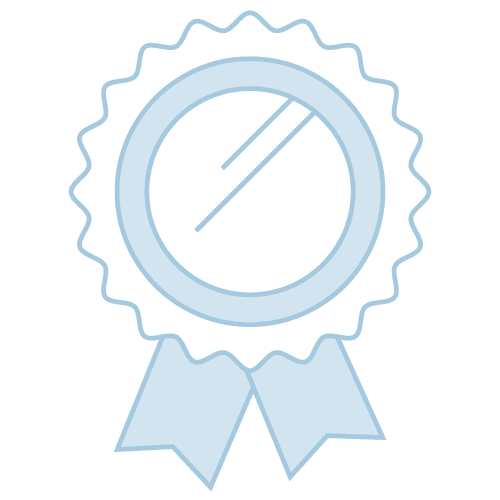