How to align Digital Analog to 3D printed model of dental implant: CAD/CAM Digital Planning
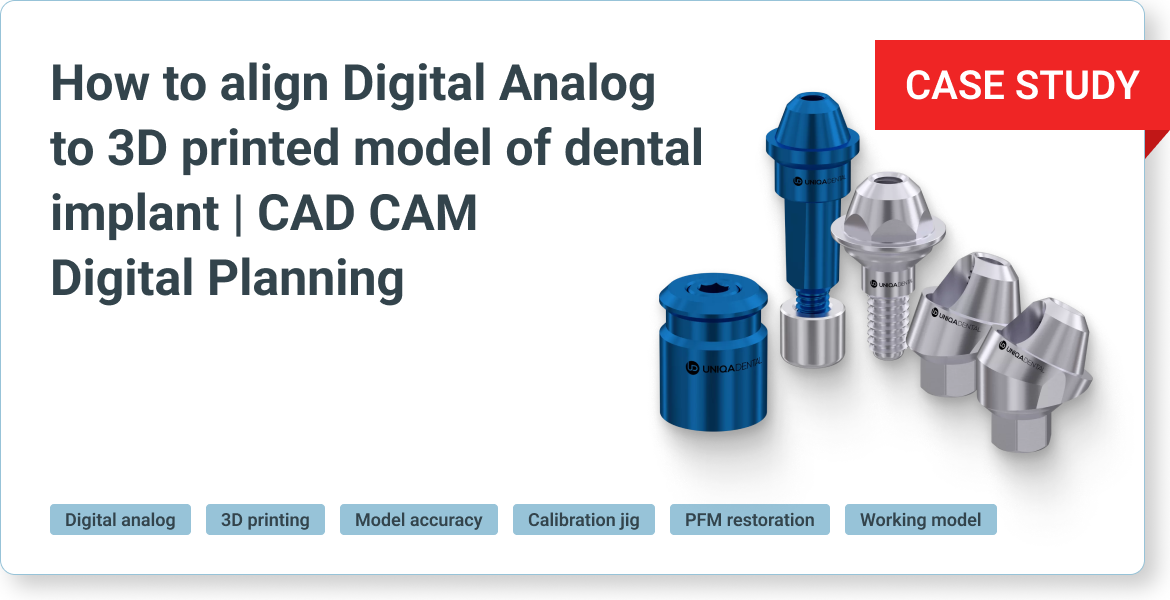
The patient’s problem
Today’s discussion will not focus on this specific case; rather, it serves as an illustrative example of the application in question. The case at hand demonstrates the necessity for precise and accurate models in CAD/CAM usage, particularly when fabricating a PFM (Porcelain Fused to Metal) restoration. The dental technician requires a metal framework as a reference to design the porcelain overlay. Consequently, it is imperative to have high-quality digital analogs that align perfectly with the printed model.
Our experience across various companies has highlighted that while digital analogs may be of good quality, discrepancies often arise due to the use of different materials and printers by technicians. Such variations can result in analogs that fit well, fit loosely, or do not fit at all, with no existing solution to rectify these issues. Today, a method that has been developed to address this challenge using specialized libraries will be introduced. In the current case, a temporary restoration on the upper jaw made from PMMA is observed, showcasing problematic teeth on both sides.
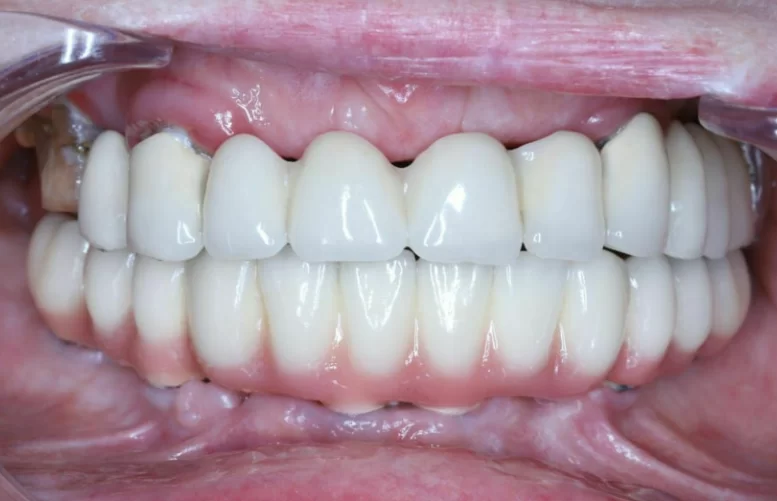
Temporary prosthesis made of PMMA plastic – the patient’s living teeth affected by caries are visible on the sides
It is evident that the current restoration is provisional. Notably, carious lesions are discernible even beneath the bridge. The affected teeth will require extraction.
Now, the existing bridge is removed and the dentists proceed with the extraction of the designated teeth. At this juncture, it becomes necessary to initiate the implantation process. The strategic placement of implants will occur in both the anterior and posterior regions. Following the implant placement, suturing is performed. This sets the stage for the subsequent selection of appropriate multi-unit abutments and taking impressions for the final restoration.
Upon completion of the impressions, a critical phase is encountered: the creation of a working model. This model is particularly crucial when fabricating a Porcelain Fused to Metal (PFM) prosthesis. In contrast, for monolithic zirconia restorations such as single crowns or small bridges, a physical working model is often unnecessary. The digital model in your computer suffices, as these restorations require only glazing and minimal coloring without additional ceramic layering.
However, for restorations that necessitate ceramic application, as well as for PFM cases, a tangible working model is essential for verification, adjustments, and visualization purposes. The challenge in CAD/CAM processes lies in translating digital data into a physical form. The working model, typically constructed from plastic, must incorporate digital analogs that precisely match the printed model. If the digital analogs do not align accurately, the bridge designed on the digital model may not fit the physical working model. This case illustrates the importance of a scan to ensure the fidelity of the working model to the digital design.
The scan reveals the presence of six upper implants, which could be referred to as an ‘all-six’ case. Visible are the scan abutments, indicating that the impression was captured at the multi-unit level. The objective now is to create a working model from this data to facilitate the fabrication of a PFM prosthesis.
The clinician’s preference for the final restoration is a PFM. The envisioned outcome is a two-part PFM consisting of a base that mimics the gingiva, complete with screw channels, and individual crowns that will be affixed to this base. The design aims to achieve both functional integrity and aesthetic harmony with the patient’s natural dentition.
The final restoration will consist of PFM crowns, necessitating the use of a precise working model. The nature of this work requires frequent insertion and removal of the base and crowns, thus the working model must be of exceptional quality and adhere to high standards. The challenge lies in procuring such models. In this instance, the clinician has ingeniously designed the working model in two distinct parts, with the gingiva component being printed independently.
The foundation of the working model is made of durable plastic, which may exhibit variations when printed with different printers or materials. Such discrepancies can arise from the material’s shrinkage factor, which is particularly relevant for larger models. Given the substantial height and size of the model, precise calibration of the analog’s placement is essential. This calibration must account for the specific model, printer, and material in use. It is advisable to recalibrate each time there is a change in the printer or a transition between materials to ensure accuracy and consistency in the final product.
How to improve the accuracy of manufacturing a physical model
Upon downloading our library, you’ll find in its folder a space of scaling.
The term ‘space of scaling’ refers to the array of spacers that surround the nominal spacer. For instance, the normal spacer is designated as 1.0. Depending on the requirements, one may opt for a spacer that is either smaller or larger than the nominal value. Accompanying these spacers is a calibration jig.
It is a tool with four distinct calibration settings, each featuring a variety of holes to accommodate different spacer types. This device is particularly useful for those utilizing analogs for internal hex implants. It contains five holes, each corresponding to a different spacer size, clearly labeled for identification.
To utilize this tool, one would print the calibration block and proceed to test the fit of their analog with each hole. The hole that provides the best fit indicates the appropriate spacer file to use. This file should then be transferred to the primary library folder for consistent use. It is crucial to recalibrate whenever there is a change in material, printer, or printing technique to ensure optimal results.
This calibration process is vital for achieving precise fits for various printed dental components, such as gingiva, temporary models, temporary bridges, and the final model. Proper calibration ensures that each component fits accurately, mirroring the intended fit within the patient’s mouth.
Calibration is essential at every stage to maintain the highest level of accuracy. By doing so, the fit between the analog and the model remains consistent, and the designed bridge will align perfectly with the original patient scans. This meticulous approach is key to preserving the precision of the initial positioning throughout the impression and modeling processes.
Scanning the working model is not advised under any circumstances. It is a groundbreaking method to enhance the precision of analogs significantly. This solution is remarkably straightforward: simply print the calibration box and insert it. There is no need for adjustments to the printer settings; all modifications are managed within the exocad library. This convenience allows for seamless transitions between different printers and materials without external assistance.